Baha, These are what i use for grinding and finishing. To the right is what i use to knock down everything smooth. Its an 80 grit quick change sanding pad. Works wonderfully. These have a seperate piece that mounts them to the grinder. Best money every spent in my opinion. They are not cheap but damn they work great. I will not use a grinding rock. Worst money ever spent in my opinion. I dont like the roloc disk because they are flimsy and you cant bare down any at all or shape the disk to the metal and work it. To the left is an 80 grit flap disk that i use to buff with for a finished product. The reason i buff everything so smooth is because these gates are powdercoated. Meaning that there is absolutely no bondo or filler of any sort in any of my gates. If tubing doesnt match up perfectly i step beads down and grind and repeat until i have a smooth surface with no dips. The circle piece in the cut out gate, after being bent was a quarter inch larger than the other tubing. So after splitting the difference i had an 1/8" drop from circle tubing to other tubing. I walked it down until its smooth and you cant even tell it
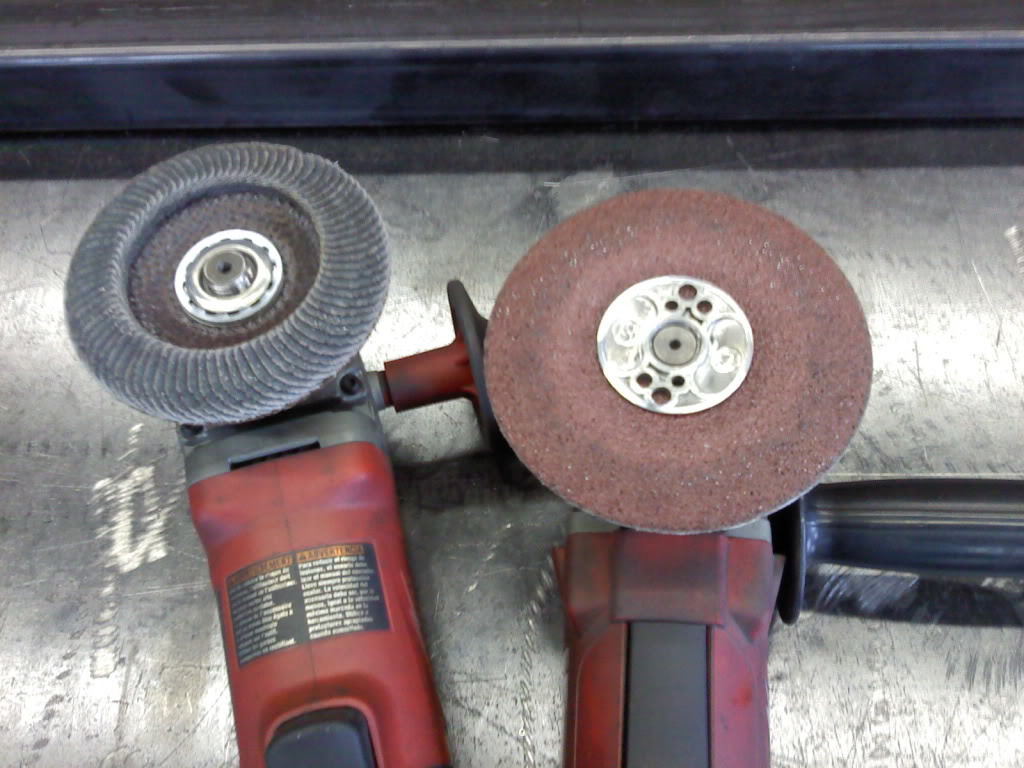
-Justin